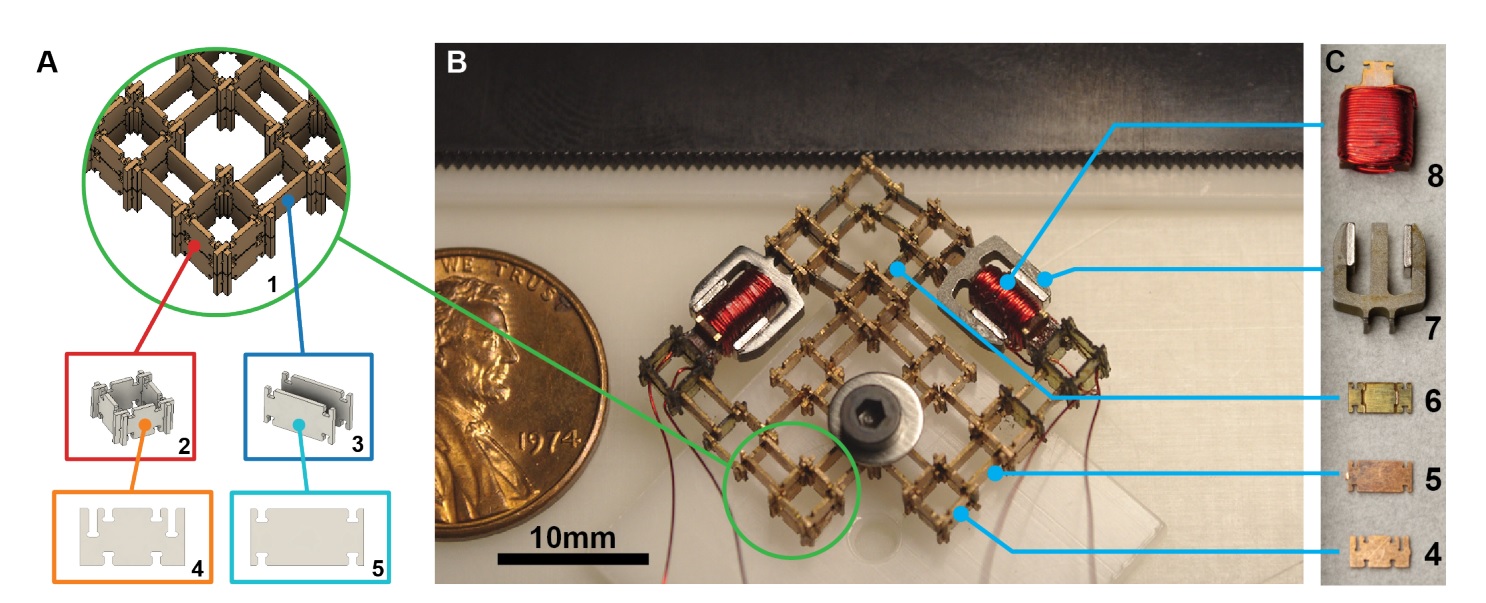
A MIT robotics research team has created micro robots that can be easily reassembled to perform different functions.
The microrobotics that are being developed by MIT Professor Neil Gershenfeld consist of five fundamental parts that can be rearranged into an array of devices.
The current trend in developing robotics roughly falls into two categories; custom designed machines for use in manufacturing processes such as assembly arms or welders, these tend to be expense and not easily repurposed. While on the flip side ones that can be reconfigured or repurposed are often not as efficient, as they are not designed with one particular task in mind.
The new robotics designed by the team at MIT are a set of five millimetre-scale components that can all be interconnected via a standardised connection. The component parts include rigid and flexible types, as well as an electromagnetic parts, coils, and a magnet.
MIT Robotics
With this toolbox of components, the researchers are able to create micro robots that can move appendages in mechanical steps allowing them to move across a space, or interact with objects such as a gear wheel. Due to the design of the kit the microrobotics can be assembled into other configurations such as hands for gripping and legs for movement.
The motor in the microrobotics is capable of lifting seven times its own weight, but due to the Lego like nature of the robotics new parts can be patched into to give it more strength. A key advantage of the design is that they can be used in small confined spaces as some robotics are no bigger than an American penny or just under 20mm in diameter. Something that size could potentially be instrumental in a search and rescue operations following a building collapse.

Sergej Fatikow, head of the Division of Microrobotics and Control Engineering, at the University of Oldenburg in Germany independently commented on the research that: “Standardization is an extremely important issue in microrobotics, to reduce the production costs and, as a result, to improve acceptance of this technology to the level of regular industrial robots.”
He said that the MIT work: “Addresses assembling of sophisticated microrobotics systems from a small set of standard building blocks, which may revolutionize the field of microrobotics and open up numerous applications at small scales.”
“We built a Discretely Assembled Walking Motor (DAWM) to demonstrate the integration of structure, mechanism, and actuation. The DAWM system takes small cyclical steps to produce long range motion of a sliding or rotating element” the research team said in a paper published this week.
“This principle of locomotion is most commonly used with piezoelectric actuators for applications such as nanometerprecision stages and focusing motors in DSLR cameras,” they added, concluding: “We have shown that machines with integrated mechanisms and actuation can be assembled from a small set of building blocks”.