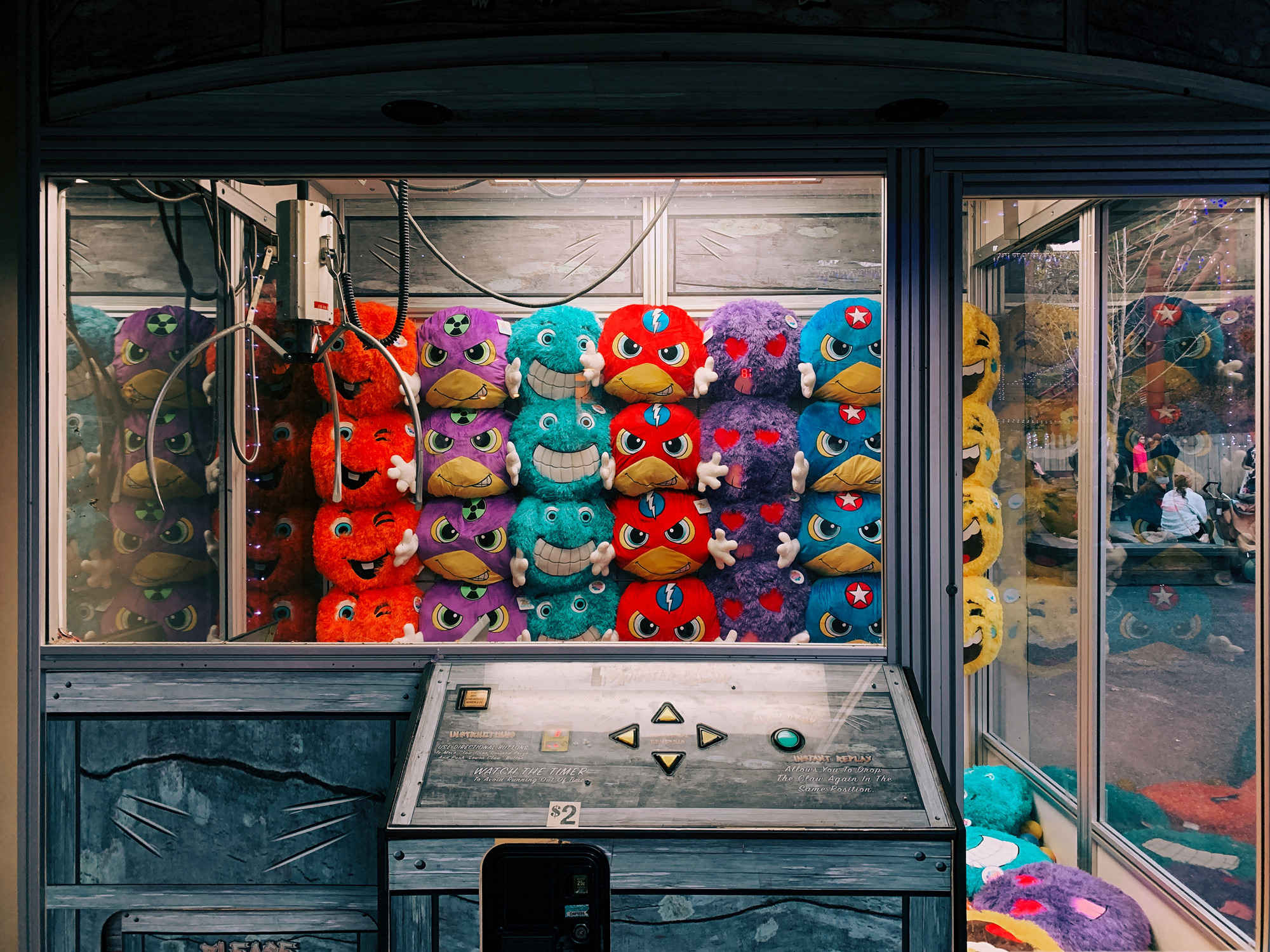
MIT researchers have created an innovative way to manipulate objects that are a 1000 times smaller than a human hair: an adhesive gripper that could be used to create densely packed circuit boards and place microscale LED pixels.
Semiconductor companies are moving further into the lower reaches of the nanometer scale in order to create densely packed chips and circuit boards.
One new approach has seen the creation of ‘chiplets’, components used in the creation of semiconductors and single chips. Chiplets are small pieces of silicon placed onto chips in a modular fashion to create a larger integrated circuit block.
As these chiplets and the silicone particles constituting them get smaller in scale, our ability to move them around is reaching a limit. The MIT researchers have created an ‘electroadhesive stamp’ that can pick up objects at nanometre scales and could be highly useful in the fabrication of nanometre chips and circuits.
Sanha Kim, a former MIT postdoc and research scientist working on the technology commented in a blog: “Electronics manufacturing requires handling and assembling small components in a size similar to or smaller than grains of flour.
“So a special pick-and-place solution is needed, rather than simply miniaturising [existing] robotic grippers and vacuum systems.”
To tackle this problem, the researchers have created a ceramic coated nanotube gripper that uses electronic polarisation to pick up and drop objects at the nanometer scale. This electroadhesive printing technology could be scaled up to help manufacture circuit boards and miniature electronic chips.
Manipulates Micro Objects
A nanometer is a billionth of a meter, to give that context a sheet of paper is roughly 100,000 nanometres thick, while a human hair is 80,000. The smallpox virus that infects the human body ranges from 300 to 350 nanometres.
Current mechanical grippers are limited to manipulating objects no smaller than 1000 nanometres. But using their electronic adhesive stamp the researchers were able to pick up objects that were just 20 nanometres wide. The placing of electronic components at the nanometre scale is often done using a gravity-assisted drop, but the smaller the scale you go the more likely surface forces will win over gravity.
Professor John Hart mechanical engineering associate at MIT commented that: “The dominance of surface forces over gravity forces becomes a problem when trying to precisely place smaller things — which is the foundational process by which electronics are assembled into integrated system.”
His researcher team created a gripper by coating carbon nanotubes, rolled carbon atoms, with a layer of aluminium oxide, plus a ceramic layer.
Once a voltage is applied to the nanotubes the ceramic layer becomes polarized. This polarisation causes the tubes to have a ‘stickiness’ quality that is used to pick up objects as small as 20 nanometres wide. Once the voltage is turned off the gripper essentially drops the object in place.
Professor John Hart mechanical engineering associate at MIT commented that: “With ever-advancing capabilities of semiconductor devices, an important need and opportunity is to integrate smaller and more diverse components, such as microprocessors, sensors, and optical devices.
“Often, these are necessarily made separately but must be integrated together to create next-generation electronic systems. Our technology possibly bridges the gap necessary for scalable, cost-effective assembly of these systems.”